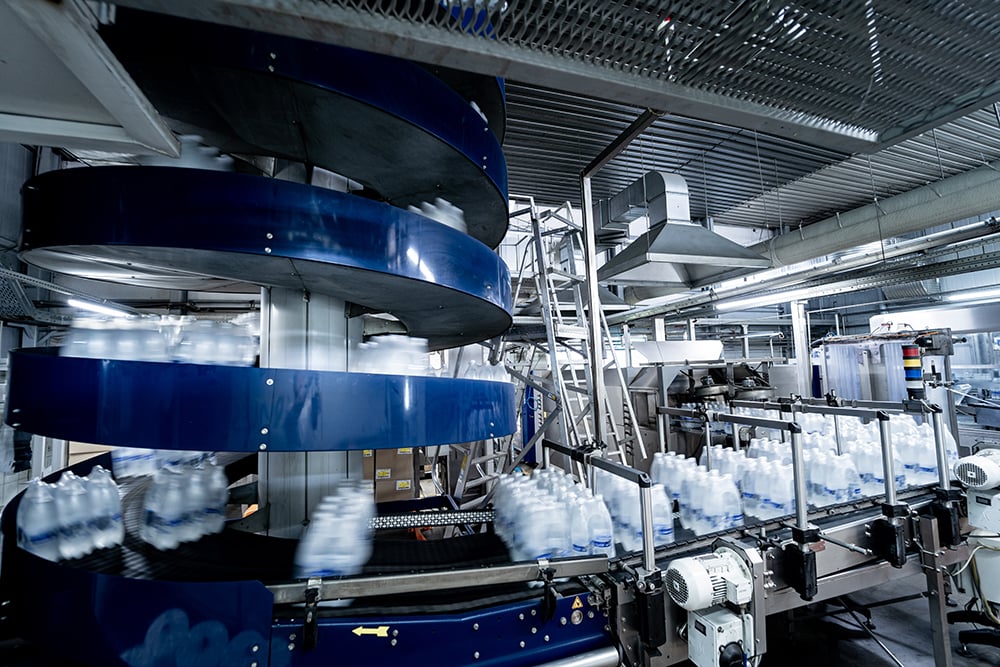
In today’s global economy, changes in trade policy can have ripple effects across manufacturing industries. Tariffs, which are taxes imposed on imported goods, were once a forgotten issue for valuation professionals; however, with the current administration’s policies potentially taking a more permanent effect, the impact on equipment markets can be significant. From a valuation perspective, how this will influence values, resale dynamics, and replacement costs will eventually factor into the analysis.
One of the most direct effects of tariffs is the increased cost of new machinery and equipment, particularly when key components or entire machines are imported. As prices for new equipment rise due to tariffs, the value of used equipment may also increase, particularly if buyers turn to the secondary market to avoid the higher cost of buying new. For equipment appraisers, this means staying on top of evolving price trends and factoring in market scarcity or shifts in buyer behavior.
From another perspective, higher equipment costs can lead to a slowdown in capital investment, especially in price-sensitive sectors like agriculture, construction, and manufacturing. If tariffs squeeze margins or disrupt supply chains, companies may delay equipment purchases or scale back expansion plans. This can soften demand in the used equipment market, making certain assets harder to sell and thus reducing their fair market value.
Tariff announcements and trade disputes can cause sudden changes in manufacturer pricing, buyer sentiment, and business owner inventory levels. This volatility makes it harder for appraisers to rely on historical data and will create a need to understand how this current activity could impact used equipment values. Steel and electronics industries, for example, could affect transportation and machine tool industries in more subtle ways; therefore, appraisers should keep an eye on tariffs for parts that are critical components for these types of machines.
There are usually delays with the full after-effects of changing global trade policy. Therefore the appraiser should consider the effective date of their analysis and whether these effects are going to be a short-term or long-term issue.
In summary, the equipment appraiser’s role becomes even more essential during periods of economic uncertainty. Tariffs can shift the balance between domestic and international equipment markets, affect demand for used assets, and inject volatility into pricing data. By monitoring market reactions and staying informed about global trade developments, equipment appraisers can continue to deliver credible, market-sensitive valuations.